Ensuring Safety and Efficiency: The Importance of Containment Systems in the Pharmaceutical Industry
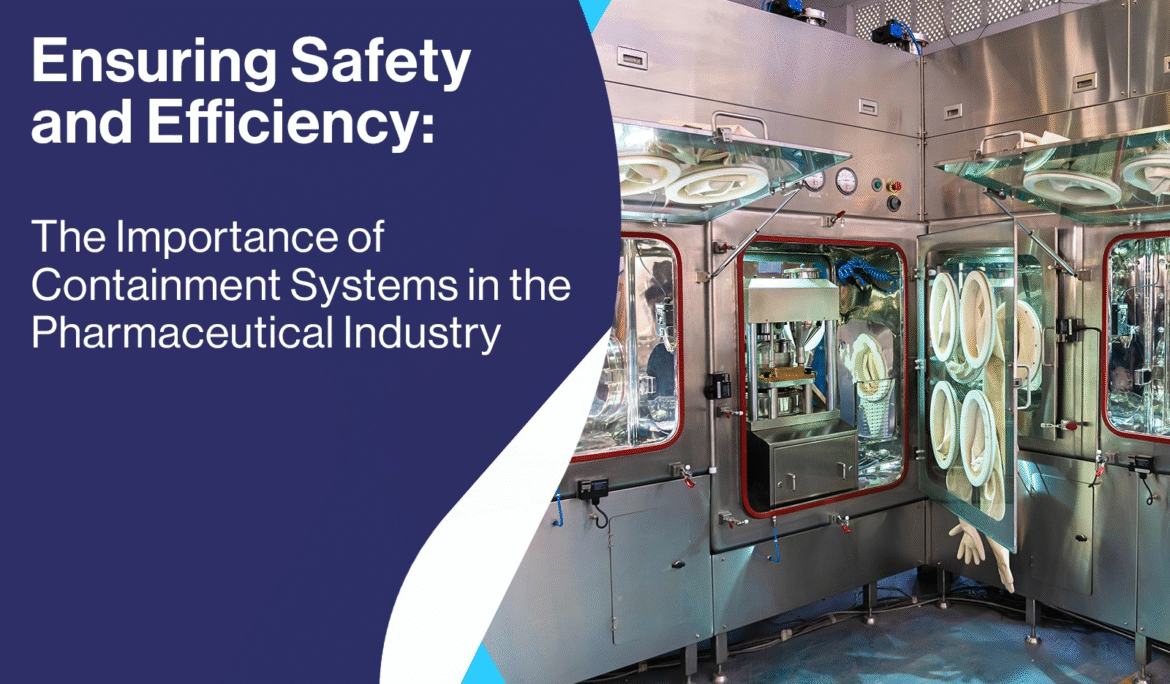
Containment systems have been in use in the pharmaceutical industry for several decades. They play a crucial role in making the manufacturing process safe and efficient. Effective containment in pharmaceutical manufacturing ensures clean processes, safe environments, and regulatory confidence.
What is a containment system?
A containment system for pharma, also known as a pharma isolator, is an enclosed structure primarily made of SS 316L. It is designed to provide a controlled environment for handling hazardous substances or materials. It serves as a barrier between the operator and the product, preventing the potential release of harmful contaminants and promoting operator safety in pharmaceutical plants.
History of the containment system in pharmaceutical manufacturing:
The need for increased safety measures became apparent with the rise in the production of potent drugs, such as cytotoxic or highly active pharmaceutical ingredients (APIs). The first aseptic containment system was introduced in the 1980s as a response to this emerging need. Containment technology in pharma has evolved significantly to meet the changing demands of the industry.
Containment system advantages in pharma manufacturing:
Today, the pharma containment systems are extensively used for several reasons, such as
- Protection of Personnel: Containment systems for the pharmaceutical industry ensure the safety and well-being of workers by minimising their exposure to hazardous substances, such as potent drugs, toxic chemicals, or biological agents.
- Product Protection: Contamination of pharmaceutical products can compromise their quality and efficacy. Hence, cross-contamination control in pharma manufacturing is critical. High containment isolators safeguard the integrity of the product by minimising the risk of contamination during manufacturing, processing, and packaging.
- Regulatory Compliance: The pharmaceutical industry is heavily regulated to ensure adherence to strict quality standards. The use of containment solutions helps pharma companies comply with regulatory guidelines and demonstrate a commitment to patient safety. For example, GMP-compliant containment systems are essential for regulatory approval and consistent product quality.
Read More: Containment System Manufacturer and Solutions with Their Benefits
The Different Types of Pharma Isolators:
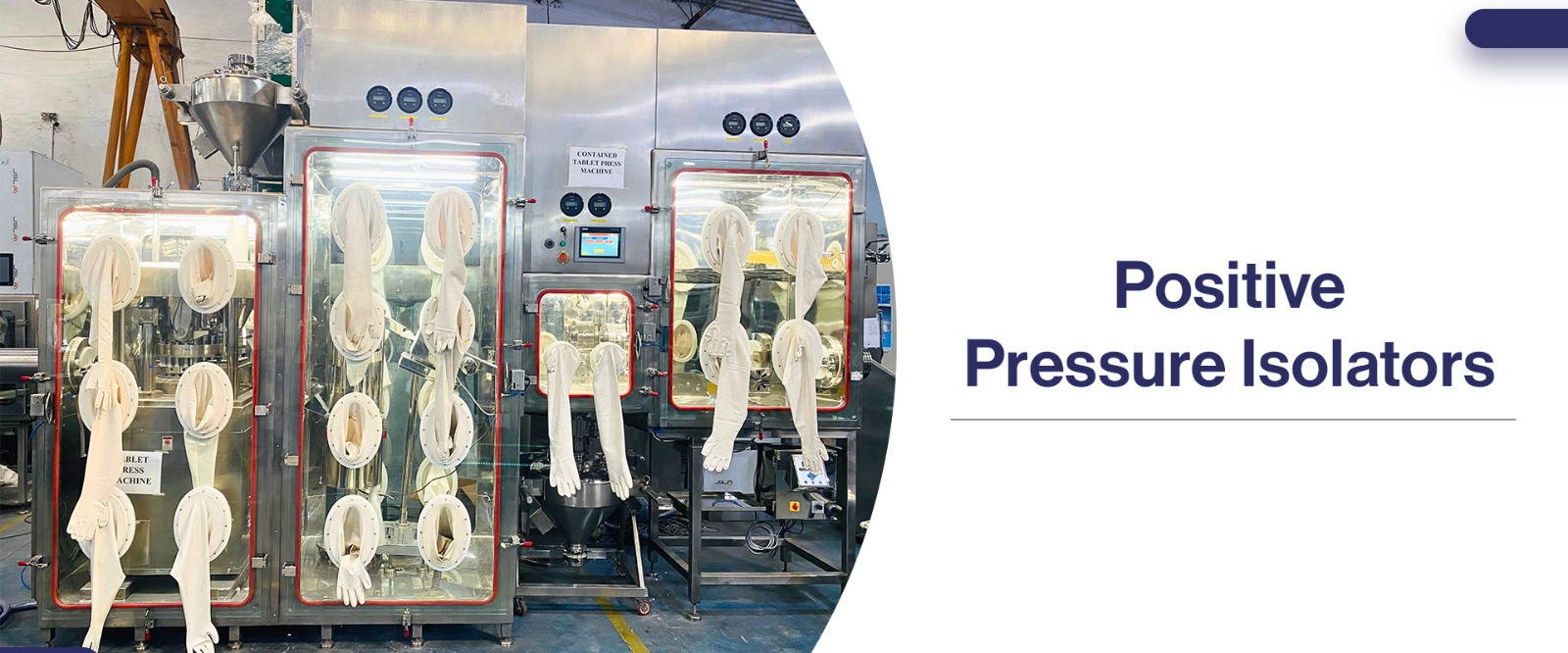
1) Positive Pressure Isolators:
Positive pressure isolators are a containment technology in the pharma industry that maintains a higher pressure inside the enclosure compared to the surrounding environment. This positive pressure creates an outward flow of air, preventing contaminants from entering the system.
a) Air Supply: The isolator is equipped with a dedicated air supply system, typically incorporating high-efficiency particulate air (HEPA) filters.
b) Airflow Management: The filtered air is introduced into the isolator, creating a positive pressure. This positive pressure creates a continuous outward airflow, pushing any potential contaminants away from the critical process area.
c) Operator Protection: Positive pressure isolators provide operator protection by ensuring that the air within the enclosure is constantly flowing outwards. This flow of air forms a protective barrier, preventing external contaminants from entering and potentially exposing the operator to hazardous materials.
d) Product Protection: By preventing airborne particles, microorganisms, or other contaminants from entering the system, positive pressure isolators safeguard the integrity of the pharmaceutical product being manufactured or handled
2) Negative Pressure Isolators:
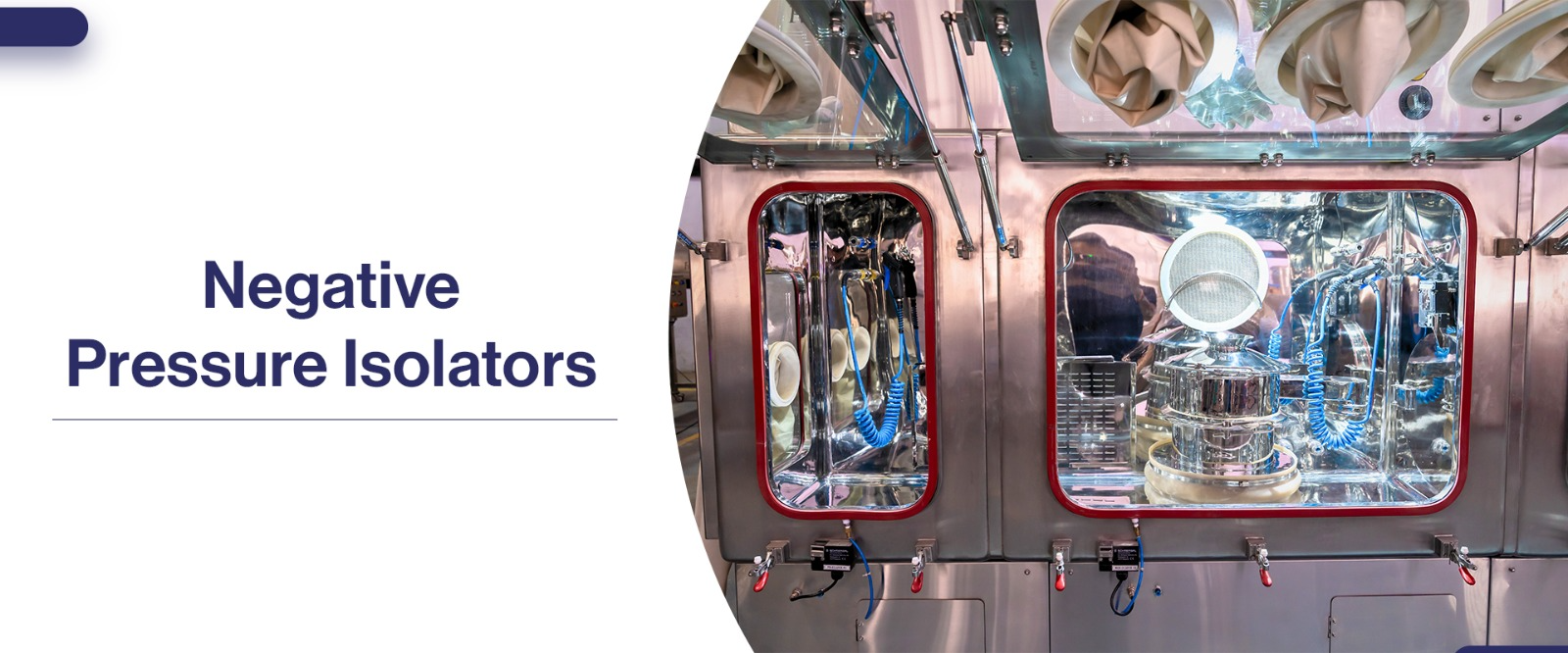
Negative pressure isolators are a pharmaceutical containment solution that operates on the principle of maintaining a lower pressure inside the enclosure than the surrounding environment. This negative pressure prevents the release of hazardous substances into the surrounding area, providing protection to both personnel and products.
a) Air Extraction: Negative pressure isolators are equipped with an exhaust system that continuously draws air from the enclosure. This air is typically passed through HEPA filters to remove any airborne particles or contaminants before being released into the external environment.
b) Airflow Direction: The negative pressure inside the isolator creates an inward airflow. This ensures contaminants are contained & prevented from escaping the isolator chamber.
c) Operator and Environmental Protection: By maintaining a negative pressure, these isolators prevent the release of contaminants. This helps achieve operator safety in pharmaceutical plants and limits exposure to toxic substances in the surrounding environment.
d) Product Protection: The inward airflow helps maintain a clean and controlled environment, ensuring the integrity of the pharmaceutical product.
3) Restricted Access Barriers (RABs):
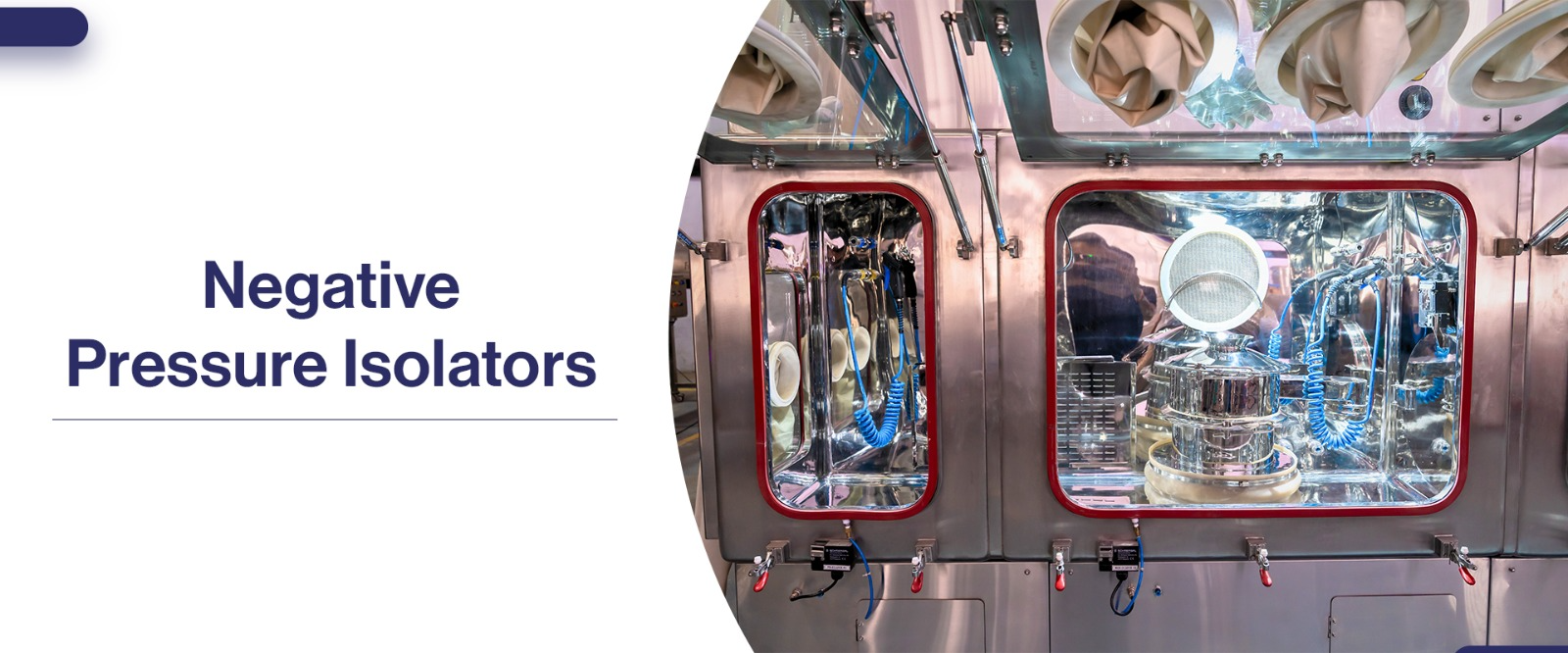
Restricted access barriers, or RABs, are partial enclosures that provide a physical barrier between the operator and the process while allowing interaction with the product. RABs offer a higher level of operator mobility and flexibility compared to a fully enclosed pharma containment system..
a) Physical Separation: RABs are designed to create a physical separation between the operator and the hazardous process by making use of transparent panels or screens that allow the operator to visually monitor and access the process.
b) Glove Ports: RABs incorporate glove ports through which the operator can reach inside the enclosure to handle the product or perform necessary tasks. These glove ports are equipped with gloves made of appropriate materials to ensure compatibility with the process and prevent cross-contamination.
c) Airflow Control: RABs may have local exhaust ventilation systems to capture any potential airborne contaminants generated within the enclosure.
d) Flexibility and Mobility: RABs offer greater flexibility for operators to access the process and perform tasks while maintaining a level of containment. This allows for easier manipulation of containment equipment for pharma, sampling, or other necessary operations while reducing the chances of cross-contamination.
Conclusion:
As drug formulations become more potent and pharma manufacturing standards become more stringent, advanced containment technologies are essential. In fact, we believe that it’s what the future of pharma will be built on.
F Plus Healthcare Technologies is a pharma isolators manufacturer supplying containment systems to pharmaceutical companies across the globe, including countries such as Thailand, Vietnam, Russia, the Philippines, Turkey, KSA, Iran, Iraq, Palestine, Syria, UAE, Algeria, and many more.