In-Depth Insights into Tablet Formulation Techniques
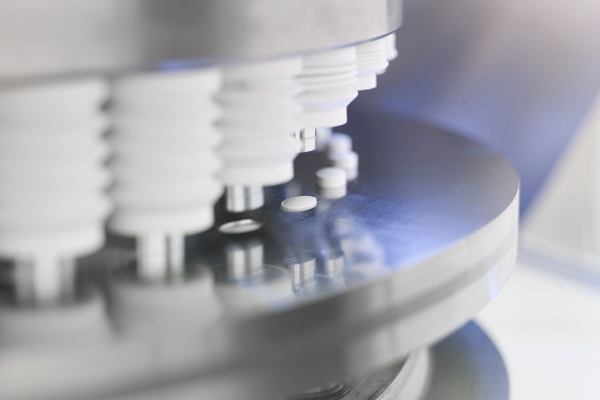
Tableting represents a range of processes used to transform a powdered formulation into solid tablet form.
Formulation Phase
The initial phase involves creating the tablet’s formulation, a critical step, particularly for pharmaceutical-grade tablets containing active pharmaceutical ingredients (APIs). Here, meticulous attention to ingredient ratios is crucial. Excipients or “fillers,” including binders, diluents, lubricants, and disintegrants, are often present. The percentage of API in the final tablet is known as the “drug load.”
Granulation Techniques: To ensure the optimal particle size distribution for effective tablet formation, the powder material often undergoes granulation. There are two primary granulation methods:
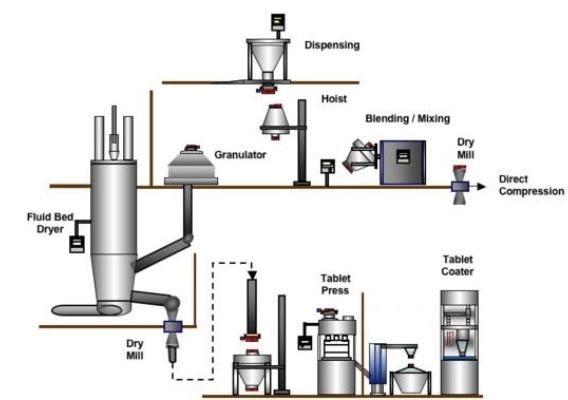
Wet Granulation: This common technique involves introducing a liquid binder to the powder mixture, which is controlled through drying in a fluid bed dryer.
Dry Granulation: Dry granulation aims to achieve a granular texture similar to wet granulation without the use of fluids. This is accomplished through slugging or roller compaction. Slugging involves using a static press to form slugs from the powder, which are then milled into a granular, uniform texture. Roller compaction utilizes rotating rollers to compress smaller particles into a ribbon or sheet, rather than slugs. This method typically allows for faster processing and greater control over compaction pressures.
Granulation’s Role: Granulation plays a pivotal role in ensuring the powder’s free-flowing quality into the hopper, a crucial factor in producing high-quality tablets.
Transferring material from the Granulation Suite to the tablet compression machine is a pivotal step in tablet production:
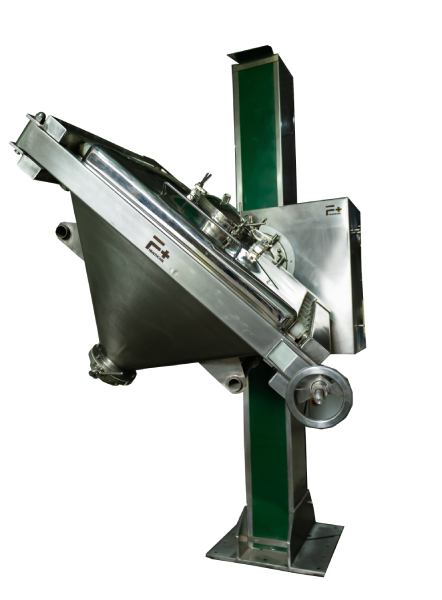
Gravity Based Transfer: For small-scale operations, granulated material is collected and transported manually to the machine’s hopper.
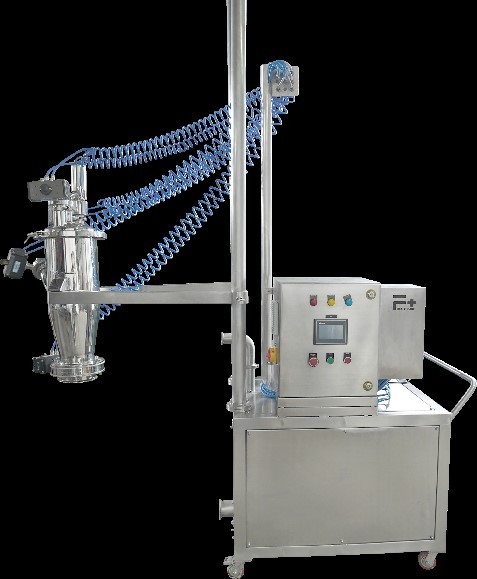
Automated Transfer: In larger facilities, automated systems like conveyors or robotics move containers to the machine and handle precise loading.
Closed Transfer: When dust free transfer is paramount, closed systems maintain ideal conditions, ensuring product integrity. These systems use sealed containers and airtight connections to transfer the material.
Adherence to GMP and SOPs is essential across all transfer methods to maintain quality and safety. The choice depends on production scale and product characteristics.
Tablet Forming Process: Tablet formation in a compression machine involves feeding granulated or powdered materials into a hopper, ensuring proper flow for uniform composition. A metering mechanism accurately dispenses the material into die cavities. Compression via upper and lower punches shapes the tablet, followed by ejection.
Critical factors for tablet quality include material properties (flowability and consistency), well-designed die cavities, precise compression force, uniform granulation, appropriate lubrication, machine calibration, and skilled operator oversight.
Optimising these factors ensures the consistent production of high-quality tablets in pharmaceutical manufacturing.
Tablet Press Components: Tablet presses share common components, which include:
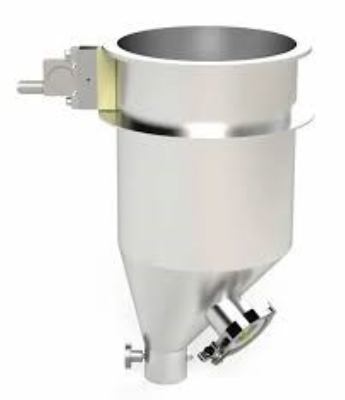
Hopper: This component holds the powder material before the tableting process.
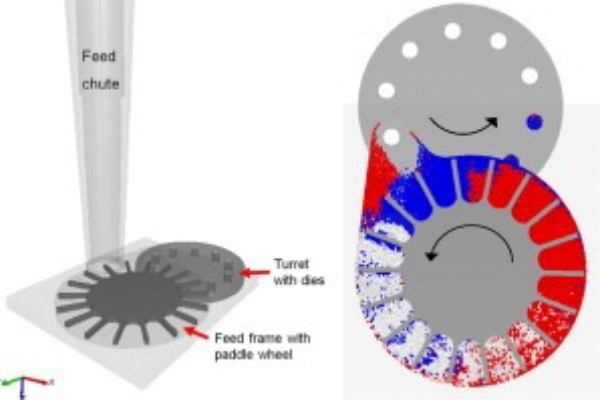
Feeding Mechanism: It connects the hopper to the cavity, facilitating the movement of powder material into the cavity.
Die: The die’s cavity determines the tablets’ shape.
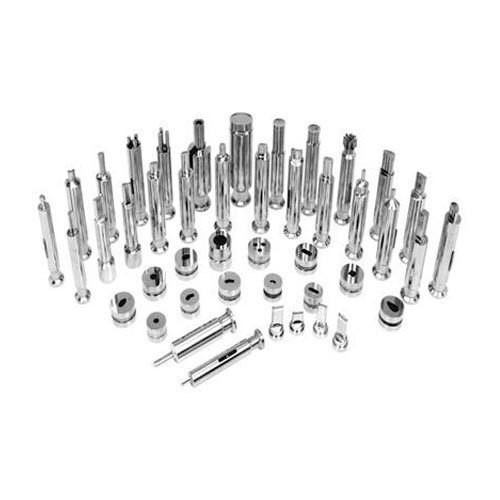
Punches: Both upper and lower punches exert vertical force on the die, causing the powder to compress and take the cavity’s shape.
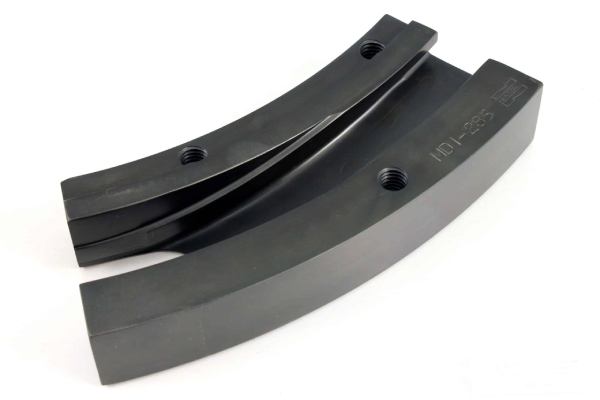
Cam Track: The cam track governs the movement of the punches.
Variations in Tablet Presses: Tablet presses can be configured in various ways to suit different tableting volumes. For example:
Multiple Station Tablet Presses: These rotary tablet presses employ a rotating turret with upper and lower punch rings/punches and a die table. Cams and cam tracks ensure that the punches operate in a controlled and predictable manner during filling, compression, and ejection.

In some cases, a tablet coating machine is used to coat the tablets (sugar, film, enteric). The tablet coater ensures evaporation of any solvent used in manufacturing the tablets.
F Plus Healthcare Technologies proudly offers cutting-edge tablet compression machines and accessories designed for modern pharmaceutical needs. Our machines are versatile, capable of seamless integration into central systems or independent operation, providing flexibility to our valued clients. Moreover, they adhere to the highest industry standards, including 21 CFR Part 11, EU-GMP, and US-FDA compliance. We cater to pharma industries across the globe, providing quality machines and equipment to regions like Turkey, Tunisia, Russia, Syria, and Vietnam and many more. To discover more about our advanced machinery and its capabilities, please reach out to us at [email protected].